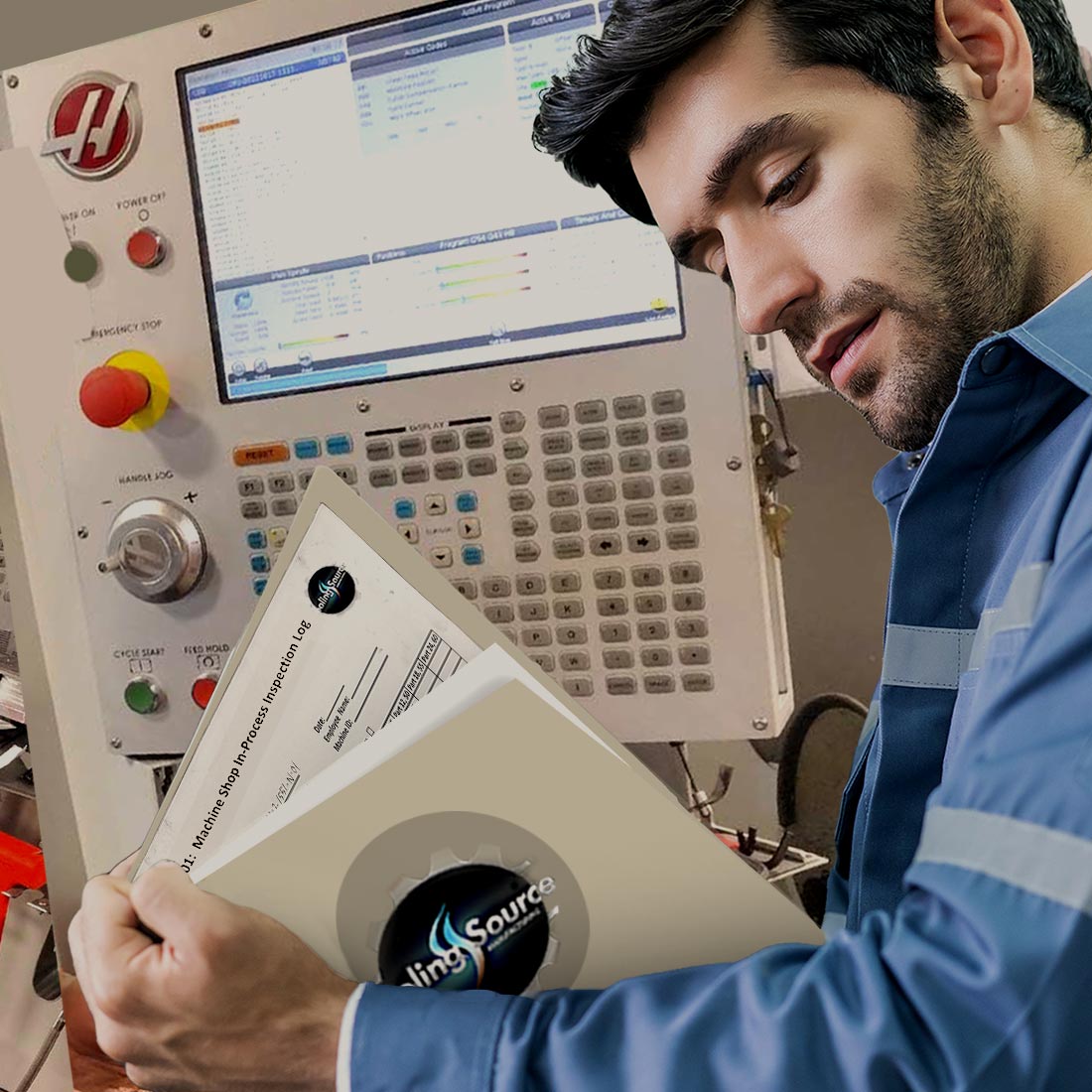
How Does Precision CNC Manufacturing Work? And What are the Benefits of Precise Machining
How Does Precision CNC Manufacturing Work? And What are the Benefits of Precise Machining
What is CNC machining?
What are the benefits of precision CNC machining?
- Higher Quality Products
Precision CNC machining enables manufacturers to produce higher-quality products by providing highly precise machines for their production process. This allows for improved accuracy and repeatability of machined parts, which results in greater consistency in terms of product quality. Additionally, precision CNC machining also allows manufacturers to adhere to ISO 9000 standards, which ensure that quality management practices are in place and that parts are made to the highest standards. Furthermore, by using precision CNC machines, manufacturers can avoid using non-standard material sizes, thereby helping to keep production costs low and ensuring that parts can be manufactured more cost-effectively. Finally, using precision CNC machines also helps to reduce the time it takes to get quotes, as the Design for Manufacturing feature can quickly determine if a design is suitable for production or not, saving manufacturers time and money in the process.
- Reduced Waste and Manufacturing Costs
Precision CNC machining is becoming increasingly popular in manufacturing due to its ability to reduce waste and costs. By utilizing a controlled environment to minimize the effects of heat expansion and other temperature issues on the measurement of metal parts, CNC machining allows manufacturers to produce parts more accurately and efficiently at a lower cost. By sourcing standard material sizes, manufacturers can also control costs, optimize for manufacturability, and reduce waste. Additionally, using highly precise machines for the manufacturing process allows for faster prototype production, saving time and money. Furthermore, with the trend of global trade and rising labor costs, reshoring businesses and factories can be more cost-effective. For those looking to reduce costs, the use of precision CNC machining is the right choice.
- Faster Production Times
Precision CNC machining helps to speed up production times by allowing for faster prototyping, cost-effective materials, and the ability to produce parts in a matter of weeks. With CNC machining, the production process is accelerated due to the ability to manufacture parts with more accuracy and less error. Additionally, the Design for Manufacturing feature provided by RapidDirect allows customers to assess the manufacturability of their designs as well as determining the part dimensions before manufacturing, all of which saves time in the process. Furthermore, the ability to source materials in standard sizes helps to control costs and optimize for production, resulting in faster production times.
- Improved Efficiency and Automation
Precision CNC machining improves efficiency and automation by eliminating excessive labor requirements, enabling operators to change over machining centers and run various productions, and providing repeatable results with high accuracy. This process is beneficial for the automotive industry as it allows for functional market testing and changes to the design if necessary. CNC precision machining also improves quality, as it eliminates any variation caused by manual monitoring and adjustments, and advanced software is used to meet design needs. Overall, this process helps manufacturers reduce labor costs and produce higher quality parts in shorter time frames.
- Increased Repeatability
Increasing repeatability in precision CNC machining provides a number of benefits, including improved accuracy and consistent results. By using calibrated measuring systems, a controlled environment, and a statistically valid sampling plan, CNC machining can maintain the tight tolerances and high-quality finishes required by many industries. Furthermore, repeatability ensures that multiple parts are identical and can be produced in a cost-effective manner. MSA and GR&R can help identify and correct measurement errors, thus ensuring more precise machining and better results.
- Better Material and Part Certification
Precision CNC machining helps improve material and part certification by ensuring a higher level of quality control and accuracy. Through methods such as Certificate of Conformance (CoC) to customer specifications, First Article Inspections (FAIs), Material certification and heat lot numbers, and Quality Management Systems such as AS9100 and ISO 9001, precision CNC machining is able to provide customers with greater confidence in the quality of their parts. Furthermore, these processes can help to ensure that the material used meets customer requirements and specifications, as well as industry standards. As a result, precision CNC machining helps to improve the quality and reliability of material and parts certification.
- Improved Accuracy and Tolerance
Precision CNC machining can significantly improve accuracy and tolerance in the manufacturing process by creating parts with tight tolerances. This is especially beneficial in the healthcare sector where tools such as orthotic devices, safe enclosures, implants, and MRI matches require tight tolerances. CNC machining allows for the creation of parts in a much more controlled environment, which minimizes the effects of heat expansion and other temperature issues on the measurement of metal parts. Furthermore, well-defined and controlled tolerances ensure part quality and help control costs. Additionally, precision CNC machining can help when a single part has multiple tolerances that conflict. By guiding production to a tighter, more challenging tolerance, precision CNC machining can help ensure accuracy and increase the quality of the part. Finally, precision CNC machining can be used to create precision tubing for liquid dispensing systems, which can help ensure the accuracy of fluid dispensing and testing.
- Increased Customer Satisfaction
Precision CNC machining can increase customer satisfaction by improving quality, consistency, and efficiency in manufacturing processes. By using these highly precise machines, manufacturers can produce parts that meet the highest standards, reducing the risk of defects and ensuring a more reliable product. Adhering to ISO 9000 standards also demonstrates a commitment to quality management practices, which can increase customer trust and satisfaction. Additionally, manufacturers that embrace global trade and regionalization can benefit from increased exporting and global partnerships, providing them with access to different markets and innovative solutions that can enhance customer experience. Finally, implementing a statistically valid sampling plan in quality control can provide customers with the assurance that the entire lot is acceptable. All of these factors contribute to increased customer satisfaction and a better overall experience.
- Greater Versatility
Precision CNC machining enables manufacturers to produce higher-quality products by providing highly precise machines for their production process. This allows for improved accuracy and repeatability of machined parts, which results in greater consistency in terms of product quality. Additionally, precision CNC machining also allows manufacturers to adhere to ISO 9000 standards, which ensure that quality management practices are in place and that parts are made to the highest standards…