EDM, what is the definition of Electrical Discharge Machining?
Our Electrical Discharge Machining (EDM) is a manufacturing technology that enables the fabrication of complicated shapes from tough materials with extremely tight tolerances.
Electrical Discharge Machining (EDM), or spark machining or spark erosion, removes material from a workpiece using electrical discharges (sparks).
The tool and workpiece never touch physically but are immersed in a dielectric (insulating) liquid. Voltage accumulates between the tool and the workpiece until the electric field exceeds the dielectric.
When this happens, a spark channel forms and the tremendous temperature and pressure vaporize and erode a small quantity of material from the workpiece.
About Our EDM Services
These techniques apply to all metallic and electrically conductive materials, including:
Aluminum Alloy
Stainless Steels
Nickel Alloys
Titanium
Copper
Please get in touch with us and send a print so that we can discuss your needs.
Concerning Our EDM Services
CSI’s Manufacturing provides the following electrical discharge machining services:
CNC Wire EDM
Hole Popping
Hole Drilling Machining
Advantages of this manufacturing process:
Electrical Discharge Machining (EDM) is a non-traditional machining process that uses electrical sparks to remove material from a workpiece. The benefits of using EDM include:
1. High precision: Can produce parts with very high levels of precision and accuracy, making it ideal for creating complex shapes and features.
2. Versatility: Can be used to machine a wide range of materials, including metals, plastics, and ceramics.
3. Hardness: Can be used to machine materials that are very hard or difficult to machine using traditional machining methods.
4. No tool wear: Since EDM uses electrical sparks to remove material, there is no physical contact between the tool and the workpiece, which means there is no tool wear.
5. No burrs: It produces parts with no burrs or other surface imperfections, which can reduce the need for additional finishing operations.
6. Complex shapes: It can produce parts with very complex shapes and features, including internal cavities and intricate patterns.
7. Small features: It can be used to produce very small features, such as holes and slots, with high precision.
8. Minimal distortion: Since It produces very little heat, there is minimal distortion of the workpiece, which can be important for certain applications.
Overall, EDM is a highly precise and versatile machining process that can be used to produce complex parts and features with high accuracy and minimal distortion. It is ideal for creating parts with very hard materials or very small features, and it can be a cost-effective alternative to traditional machining methods.
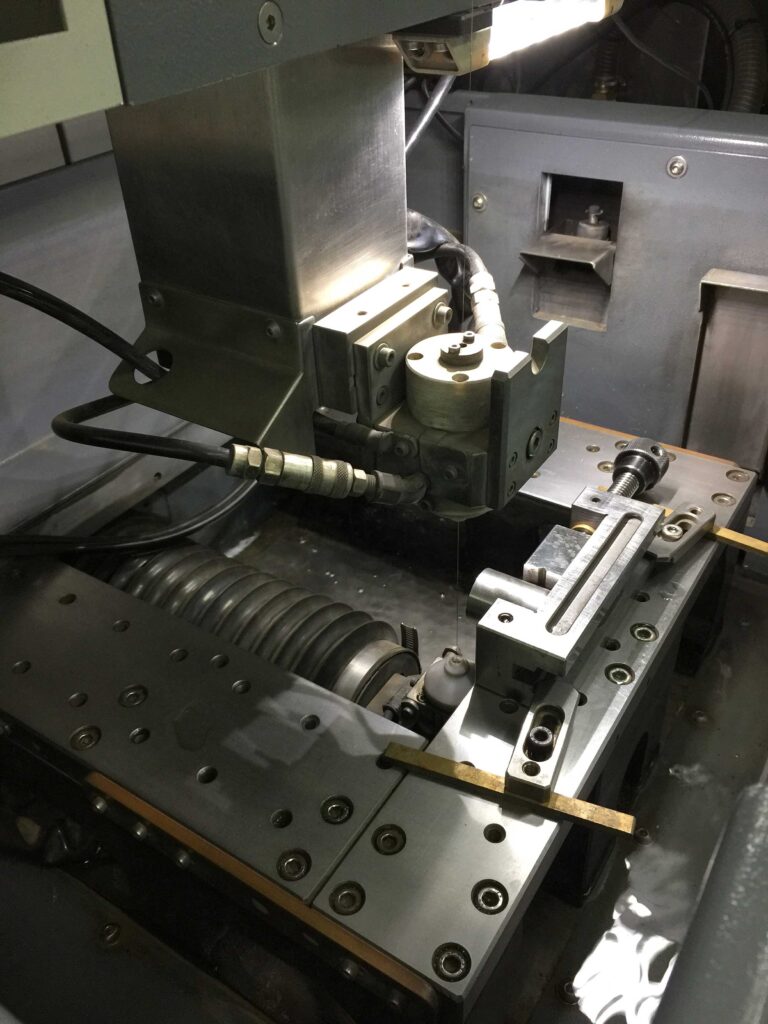
Our Partners:
ambayarea.com
thomasnet.com
Our Contact Us:
Email Us