Friction Stir Welding
Friction stir welding is a solid phase joining method with mechanical force. When the mixing head spins forward, heated metal materials plasticize from the front of the stirring head back down the transfer. With the blending head spinning slowly, friction produces friction heat. (welding temperature does not generally at and above the melting point of welding material),
Four procedures
Mechanical energy must be converted to heat energy.
Plastic deformation causes material distortion.
I am setting the pressure for the thermoplastic phenomena.
Molecular Diffusion and Recrystallization
The following are the primary advantages of friction stir welding:
First, the microstructure of welded joints does not change significantly in the heat-affected zone.
Because the residual tension is minimal, it may complete the welding of a long welding seam, large cross-section, and many locations in a single pass. At the very top:
Low energy consumption
With essential equipment, low energy consumption, high efficiency, and minimal working environment requirements, the operation process is simple to mechanize and automate:
There is no need for welding wire, no need to remove an oxidation coating before welding aluminum alloy, no need for gas protection, and the cost is modest.
Weldable heat crack-sensitive materials ideal for welding heterogeneous materials:
Friction stir welding is a non-smoking, non-polluting, and non-radioactive process.
FSW Difference
FSW’s most significant distinction is that the metal to be welded does not approach its melting point during welding. Instead, it’s like a forged in thermoplastic conditions.
Friction welding achieves the strength of the welding seam and matrix material. It has a greater welding efficiency, stable quality, and consistency. Also can weld various materials. Because of its outstanding quality, high efficiency, energy savings, and pollution-free technical advantages, friction welding is utilized in aviation, aerospace, nuclear energy, and armament. It is commonly used to connect heat sinks or to make a process flow channel for liquid cold plates. As a result, the names “friction stir welding heat sink” and “friction stir welding cold plate” were developed. The technological barrier of integrating two or more materials to manufacture high-aspect-ratio ultra-wide items can be overcome by employing friction welding for heat sinks.
Furthermore, its tooling costs are lower because of the faster cycle time and increased stability. Friction welding liquid cold plate can achieve the same thickness but a larger diameter than embedded tube flow, thus lowering thermal resistance. It is more adaptive, mainly when dealing with complex flow channels and some high and low flow channels.
Cooling Source’s friction stir welding procedure has a maximum size of 59*59 inches and a welding depth of 1.02 inches. CSI has established several standard materials based on data gathered by our R&D team over time. We are constantly expanding the database of our common materials to provide our clients with additional thermal options.
High-Quality Welding Process
FSW is a high-quality, high-efficiency, energy savings, and pollution-free manufacturing process. As a result, friction welding has become increasingly popular in new technologies and traditional industries.
Cooling Source uses friction stir welding technology to design and manufacture excellent liquid plates. Furthermore, our high-performance cold plates are ideal for high-power electronics. As a result, we provide both custom and standard cold plates with copper pipes in an aluminum base.
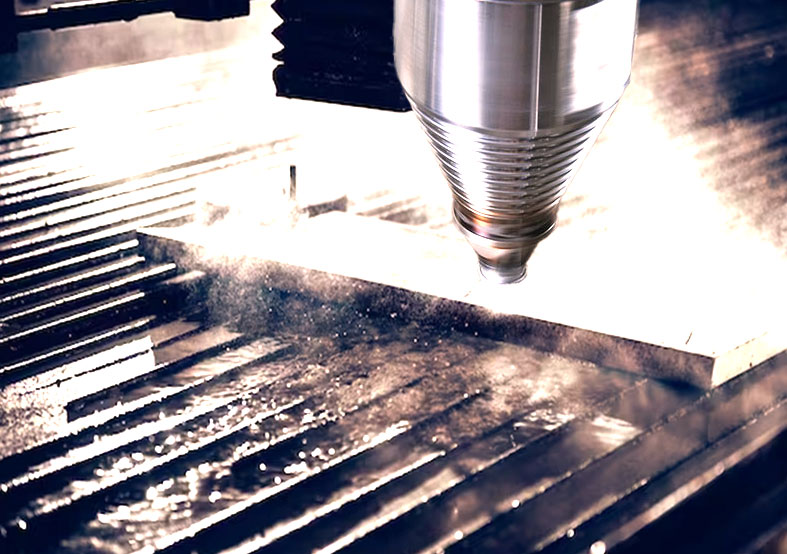
Our Partners:
ambayarea.com
thomasnet.com
Our Contact Us:
Email Us